Порошковая покраска металла была изобретена еще в 60-х годах прошлого века и очень быстро получила широкое распространение. Связано это с множеством достоинств данной технологии, таких как экономичность, экологичность, привлекательный внешний вид покрытия.
Общие сведения
Итак, смысл данной технологии заключается в том, что на окрашиваемую поверхность напыляют полимерный порошковый краситель. Именно поэтому данный метод и получил такое название. После нанесения красителя, поверхность подвергается термической обработке, в результате чего порошок оплавляется и образует сплошную равномерную пленку.
Полученное данным способом покрытие обладает следующими свойствами:
- Защитой от коррозии;
- Хорошей адгезией к основанию;
- Устойчивостью к перепадам температур;
- Устойчивостью к механическим повреждениям, в том числе и ударопрочностью;
- Влагостойкостью;
- Устойчивостью к химическим воздействиям;
- Отличными декоративными свойствами;
- Долговечностью.
Совет!
Благодаря хорошей адгезии, данный способ является самым оптимальным вариантом покраски нержавеющей стали.
Отдельно следует сказать о декоративных свойствах такого покрытия, которое отличается разнообразностью цветов и фактур, что достигается путем использования различных добавок.
В частности порошковая окраска металла позволяет получить следующие типы поверхности:
- Матовую;
- Глянцевую;
- Плоскую или объемную;
- Имитирующую золото;
- Имитирующую фактуру древесины;
- Под мрамор;
- Под серебро и пр.
Достоинства технологии порошковой покраски
Помимо возможности получения покрытия с высокими эксплуатационными качествами, данная технология обладает и рядом других преимуществ, таких как:
- Возможность нанесения красящего состава одним слоем , что недопустимо при покраске жидкими лакокрасочными материалами.
- Отсутствие необходимости использовать растворитель и контролировать вязкость материала.
- Высокая экономичность красителя , так как порошок, который не осел на окрашиваемую поверхность, можно использовать повторно. Для этого напыление выполняют в специальной камере, которая позволяет собрать весь неизрасходованный порошок. В итоге, стоимость порошковой покраски металла ниже, чем нанесение ЛКП другими способами.
- Процесс покраски занимает немного времени , причем, после нанесения краски, не надо ждать, пока она высохнет.
- Экологическая безопасность , так как краситель не содержит токсичных органических соединений. В результате отсутствует необходимость использования мощных вентиляционных систем.
- Технология нанесения красителя высоко автоматизированная , что упрощает процесс обучения работы с оборудованием.
Недостатки
Как и любая другая технология, окраска металла порошковой краской имеет некоторые недостатки:
- Невозможно устранить локальные дефекты покрытия – в случае их возникновения, необходимо полностью перекрашивать поверхность.
- Невозможность выполнения покраски своими руками, так как для этого требуется специальное оборудование и цеховые условия.
- Габариты окрашиваемых поверхностей ограничены.
- – разрешается использовать только порошковые краски по металлу от производителей.
- Невозможно окрашивать детали, которые в дальнейшем будут подвергаться сварке, так как обгоревшие участки покрытия невозможно реставрировать.
Технология порошковой покраски
Подготовка основания
Предварительная обработка является наиболее продолжительным и трудоемким этапом покраски. Однако, ей необходимо уделять особое внимание, так как от подготовки зависит эластичность, стойкость и качество покрытия.
Подготовка детали к покраске заключается в удалении каких-либо загрязнений, обезжиривании поверхности, а также фосфатировании для улучшения адгезии и защиты металла от коррозии. Очистка обрабатываемой поверхности выполняется механическим или химическим способом.
Для удаления окислов, ржавчины и окалины, эффективным методом очистки является дробеструйная очистка. Реализуется они при помощи песка, стальных или чугунных гранул.
Под воздействием сжатого воздуха или центробежной силы эти частицы с большой скоростью подаются на обрабатываемую поверхность и оббивают ее.В результате окалина, ржавчина и другие виды загрязнения откалываются от металла, что значительно улучшает адгезию.
Химический способ очистки называется травлением.
В этом случае удаление ржавчины, окислов и других загрязнений, выполняется при помощи составов на основе следующих видов кислот:
- Соляной;
- Азотной;
- Серной;
- Фосфорной.
Преимущество травления перед абразивной очисткой заключается в большей производительности и простоте применения. Однако, после данной процедуры необходимо хорошо промывать поверхность. Соответственно, возникают затраты на использование дополнительных чистящих средств.
На фото — покраска небольшой детали
Нанесение краски
После завершения предварительной обработки металла, деталь помещается в специальную камеру, где выполняется напыление красящего порошка. Как уже было сказано выше, камера нужна для улавливания неиспользованного материала. Кроме того, она не допускает попадания частиц краски в помещение.
Подобные камеры оборудованы средствами очистки, такими как бункеры и вибросито, а также системами отсоса.
Надо сказать, что камеры бывают двух типов:
- Проходные – для покраски крупногабаритных изделий;
- Тупиковые – для покраски небольших предметов.
Кроме того, существуют автоматические модели, в которых покрытие наносится автоматическими пистолетами-манипуляторами. Конечно, цена такого оборудования наиболее высокая, однако, производительность его тоже значительно выше – порошковое покрытие в этом случае наносится буквально за считанные секунды.
Как правило, нанесение краски выполняется электростатическим способом, т.е. распыляется электростатически заряженный порошок, который обволакивает заземленную деталь и прилипает к ней. Само распыление происходит при помощи пневматического распылителя, который или просто пистолетом.
После напыления порошка, изделие перемещают в камеру-печь, где оно подвергается термической обработке. Под воздействием высокой температуры порошок переходит в вязко-текучее состояние, после чего оплавленные частицы образуют монолитный слой.
Обратите внимание!
Для получения качественного результата покрытия должна строго соблюдаться инструкция по эксплуатации оборудования.
Поэтому заниматься данной работой должен специалист.
Вывод
Порошковая покраска металлических поверхностей во многом более совершенная, чем покраска жидкими красками. Однако,в ряде случаев ее применение ограничено. К тому же, выполняться она может только с использование профессионального дорогостоящего оборудования, поэтому неприменима в домашних условиях.
Дополнительную информацию по данной теме можно получить из видео в этой статье.
Немного об истории порошковой покраски
В ней не используются пожароопасные и вредные жидкие растворители, поэтому данная покраска практически безопасна как для человека, так и для флоры фауны. Отсутствие таких растворителей снижает стоимость покраски. Кроме того, выбор тонов, текстур и цветов практически не ограничен желанием и потребностью заказчика.
Порошковая покраска способна предоставить любые цвета, оттенки и фактуры: от золотистого или серебристого металлика, до поверхности под бронзу, дерево или гранит. Крася порошковой краской, получаются поверхности с различным глянцем, а также с рельефной фактурой, таких как антик или антрацит. Порошковая краска уже от колерована, что не требует таких дорогостоящих процедур как контроль вязкости и подбор тона. Это предают им наибольшую экономичность и прочность, стойкость и долговечность, и при всём этом достигается отличное качество, ровность и однотонность окрашиваемой поверхности. Порошковая покраска обеспечивает ударопрочное антикоррозийной покрытие, которое функционирует в режиме температур от 150 до -60 С и обеспечивает надежную электроизоляцию. И не реагирует на резкие перепады температур.
Порошковая краска и её экономические преимущества:
Низкий процент отходов;
На рабочую поверхность наносится до 96% краски;
При избыточном напылении, краска собирается в красильной камере и готова к очередному нанесению;
Высоко автоматизированная технология, обеспечивает легкость в уходе за покрытием, отсутствует необходимость его очистки и простоту в обучении рабочих (в основном на больших заводах); так же доступна для небольших предприятий с ручным нанесением порошковой краски.
Отсутствие очистителей и растворителей, что не требует времени на их испарение, ни затрат на удаление паров.
Порошковая краска и экология:
Отсутствуют вредные органические соединения;
Экологически чистая технология производства;
Низкая опасность возгорания;
Снижены выделения химических запахов;
Санитарно-гигиенические условия труда намного выше, чем при использовании обычных методов покраски;
В процессе полимеризации предельно допустимые нормы концентрации летучих веществ не достигаются.
Преимущества порошковых красок в сравнении с красками на растворителях:
При традиционных способах покраски невозможно достичь отличных физико-химических и декоративных свойств покрытий;
Лучшие эксплуатационные свойства, высокое качество покрытий;
Нет необходимости в грунтовки поверхностей;
Для нанесения порошковой краски достаточно одного слоя. Это достигается за счёт 100 процентного содержания сухих веществ, дорогие многослойные краски этим свойством не обладают;
В сравнении с обычными красками, порошковые краски обладают лучшими ударопрочными и антикоррозийными свойствами. Меньшая пористость в порошковом покрытии;
Так как порошковая краска поставляется в готовом виде, то не требует особой подготовки и контроля вязкости;
Потери при порошковой покраске около 2-5%, при покраски жидкими красками потери будут до 45%
Отвердевание порошковых красок составляет 30 минут;
Порошковая краска не занимает много места, поэтому не требует больших складских помещений;
Высокая прочность порошковых красок при транспортировки обеспечивает минимальное повреждение покрашенных поверхностей, что обеспечивает снижение затрат на упаковку.
Возможные недостатки:
При смене цвета, требуется чистый контейнер;
Для предотвращения взрыва требуется чёткий контроль процесса покраски;
Возникновения трудностей окрашивания очень тонких слоев;
При низких температурах, также возникают трудности в покраске;
При сборных конструкциях или нестандартных формах возникают некоторые ограничения в покраске.
Технология порошковой покраски
Есть три основных этапа технологии порошковой покраски:
1. Обезжиривание и удаление грязи с поверхности окрашиваемых изделий;
2. В камере напыления происходит нанесение порошковой краски.
3. В печи полемиризации происходит оплавление и полимерезация. Затем формируется пленка покрытия и охлаждение и отвержение покрашенной поверхности.
Лучше всего подготавливать и красить изделия на транспортной системе. На транспортной системе окрашенные изделия легко ездят от камеры напыления до печи полимеризации и наоборот. Также на транспортной системе проще подготавливать окрашиваемые поверхности к покраски. Каретки в транспортной системе легко передвигаются по рельсам. Производительность работы увеличивается, за счёт непрерывного процесса окраски на транспортной системе.
В начале процесса порошковой окраски производится подвес частей на транспортную систему. Рабочие должны понимать какие поверхности подлежат покраски, в каких местах можно сверлить технологические отверстия для подвеса деталей и как минимизировать затраты на время покраски труда и самой краски. Например, крася фасадную декоративную крышку, её можно подвешивать друг к другу тыльными сторонами, что обеспечивает меньший объем, занимаемый в печи, меньшее количество краски, т.к. краска, напыляемая с одной стороны будет попадать на другую сторону и соответственно лучшей прокрас изделия.
Затем окрашиваемые изделия подвергаются обжигу. Для этого они загоняются в специальную печь для просушки с целью предотвращения попадания на них влаги, после чего они охлаждаются.
Следующей этап размещение конструкций в камере напыления, где порошковая краска под действием сжатого воздуха и электрического распылителя наносится на окрашиваемую поверхность. Электрический заряд частички краски приобретают в распылители. За счёт этого частицы краски притягиваются к окрашиваемой поверхности и равномерно распределяются по ней.
Затем окрашиваемые детали с нанесённым слоем краски помещаются в печь полимеризации на 20 минут. Температура в печи составляет от 180 до 220 градусов, все зависит от производителя краски. Формирование поверхности происходит за счёт оплавления и закрепления на окрашиваемой поверхности. После формирование пленки покрытия детали охлаждаются и снимаются с кареток.
Самый продолжительный и трудоемкий процесс это предварительная обработка поверхности. Часто ему уделяют мало внимания, однако именно на этом этапе достигаются необходимые условия для получения качественного покрытия. При предварительной обработки обеспечивается стойкость, эластичность, долговечность покрытия, оптимальное сцепление порошковой краски с поверхностью и улучшение антикоррозийных свойств. Во первых детали нужно зачистить и обезжирить. Это достигается механическим или химическими средствами. При механической очистке используются шлеф-машины, наждачка или пескоструйные насосы, также при маленьких размерах поверхности или уже окрашенных поверхностей возможна их протирка чистой тканью, смоченной в растворителе или Уайт-спирите. Другой способ - химическая очистка, применяются щелочные, кислотные или нейтральные вещества, а также растворители. Химическая очистка в основном используется на заводах в специальных ваннах. При химической обработке детали погружаются в специальные ванны с раствором или обрабатываются струйным способом (раствор под давлением подаётся через технологические отверстия). В данном случае эффективность обработки значительно выше, поскольку деталь подвергается механическому воздействию и осуществляется поступление чистого раствора к поверхности непрерывно. После обжига детали охлаждаются естественным путём. Затем при помощи транспортной системы они подаются в красильную камеру, где и происходит нанесение порошковой краски. В камере не осевшая краска собирается для дальнейшей утилизации, либо для повторного использования. Камера оснащена системой фильтров, а также системами циклонов. Камеры бывают проходные либо тупиковые. Тупиковые камеры служат для окрашивания малогабаритных изделий, проходные – хороши в использование для покраски длинномерных изделий. На заводах широко применяются автоматические камеры напыления, в них краска наносится очень быстро с помощью пистолетов-манипуляторов.
Электростатическое напыление является самым распространенным способом нанесением порошковой краски. На заземленное изделие с помощью пульверизатора подаются электростатический заряженный порошок. Распылители сочетают в себе различные режимы:
Напряжение распространяется как вниз, так и верх. Регулируется сила факела (потока) краски и скорость её выхода. Меняется расстояние от факела до окрашиваемых поверхностей. Порошковая краска засыпается в бочок. Через перегородку бочка под давлением подается воздух, краска «закипает». Затем аэровзвесь из контейнера подаётся при помощи воздушного насоса (эжектора), разбавляется воздухом для низкой концентрации и подается в распылитель, где эта смесь за счет трения, приобретает электростатический заряд. При помощи сжатого воздуха заряженная порошковая краска попадает на нейтрально заряженную поверхность, оседает и удерживается на ней за счет электростатического притяжения. Различают две разновидности электростатического распыления: электростатическое с зарядкой частиц в поле коронарного заряда и трибостатическое напыление. При электростатическом способе напыления частицы получают заряд от внешнего источника электроэнергии (например, коронирующего электрода), а при трибостатическом - в результате их трения о стенки турбины напылителя. Заключительная стадия окрашивания происходит в печи плавление и полимеризации. Краска оплавляется и полимеризуется при температуре 180-220 °С в течение 20-30 минут, после чего порошковая краска образует пленку (полимеризуется). Основным требованием, к печи, является поддержание постоянной температуры (разброс температур в печи недолжен, превышать 5 градусов) для равномерного прогрева изделия. При нагреве в печи изделия с нанесенным слоем краски расплавляются, переходят в вязкое состояние и образуют непрерывную пленку, при этом вытесняя воздух, находящийся в слое порошковой краски. Часть воздуха все-таки остаётся в пленке, образовывая поры, что ухудшает качество покрытия. Для предотвращения появления пор покраску следует проводить при более высокой температуре, чем температура плавления краски где-то на 10-20 градусов выше, а слой краски должен быть более тонким. Для покраски больших металлических изделий, с толстостенными перегородками необходимо увеличивать время прогрева в печи, для лучшей полимеризации и адгезии.
Методы порошковой покраски
Различают четыре метода порошковой покраски: электростатическое распыление, с помощью потока воздуха (fluidized bed), электростатическое распыление с помощью воздушного потока (electrostatic fluidized bed) и нанесение с помощью факела (flame spray).
Электростатическое распыление - наиболее популярный на сегодняшний день метод порошковой покраски. Для всех прикладных методов, подготовка поверхности (то есть, очистка и конверсионное покрытие) должна создавать хорошую основу для нанесения покрытия. Поверхность должна быть подготовлена соответствующим образом. Лучшее качество нанесения краски достигается, если красить так называемой «сеткой Фарадея». Это когда изделие сначала красится вертикально по поверхности, затем горизонтально и выравнивается с небольшим отдалением пистолета в горизонтальном направлении. Рекомендуемое отдаление пистолета от окрашиваемой поверхности составляет 20-30см. Всё зависит от профиля, типа краски и настроек самого пистолета. Определение давления выхода краски, расстояние пламени пистолета от окрашиваемой поверхности и количества смешиваемой краски с воздухом может определить опытной и квалифицированный рабочий (обычно это достигается путём проб и ошибок).
Область применения порошковых красок
Порошковая покраска - это экологически чистая безотходная технология для получения высококачественных защитных и защитно-декоративных покрытий. Покрытия формируют из полимерных порошков, которые наносятся на поверхность изделия за счёт электростатического напыления. Такие покрытия, очень прочные и долговечные. Данный метод идеален для окраски кованых изделий, алюминиевых профилей и оцинкованных поверхностей.
Область применения порошковых красок постоянно расширяется. Они широко применяются в строительстве, в сельскохозяйственном машиностроении и приборостроении, автомобилестроении и других областях промышленности для окраски:
Металлические конструкции и алюминиевые профиля (двери, фасады и алюминиевые окна);
Спортивный инвентарь (велосипеды, мотоциклы и снегоходы);
Медицинской техники (кровати, стулья, столы);
Кровельных материалов (металлические кровли, водостоки);
Бытовой техники (корпуса холодильников, стиральные машины, компьютеры)
Предметов мебели;
Неметаллических изделий (предметы из гипса, керамики, стекла) и т.д.
Порошковая покраска металлических деталей своими руками – занятие не такое уж сложное, главное знать все тонкости и действовать строго по инструкции. К тому же на лицо существенная экономия средств, ведь цены в салонах по покраске частей металлических механизмов или запасных частей автомобилей достаточно велики.
Требуемое оборудование
Для того чтобы процесс самостоятельной покраски практически не отличался от заводского, необходимо выбрать подходящее место, где будут проводиться работы.
Когда помещение найдено, нужно собрать и подготовить необходимое оборудование:
- печь для полимеризации (сушки);
- источник постоянного напряжения (около 25 кВ);
- распылитель порошковой краски (пистолет);
В работе не помешает аккуратность и небольшой опыт. Но если его нет – не беда, действуя по инструкции, можно избежать большинства ошибок и получить вполне приличный результат.
Изготовление печи
Полимеризация – важный этап в отвердении порошковой краски. Если этот пункт работ опустить, ЛКМ не будет держаться на металлических поверхностях. Поэтому такое оборудование, как печь – ее еще называют камерой полимеризации – необходимо в первую очередь. Вещь эта дорогостоящая, поэтому можно сделать ее своими руками, из подручных материалов. Нам понадобятся (камера полимеризации будет иметь размеры 2х1х1 м):
- профильная труба;
- негорючая теплоизоляция (плита базальтовая);
- листовой металл (можно заказать по размерам);
- тангенциальный вентилятор;
- ТЭНы.
Инструкция по сборке печи состоит из следующих шагов:
- Сварите из профиля каркас.
- Заложите в него утеплитель.
- Листовым металлом зашейте стены. Снаружи отделайте все гипсоволокном.
- Для конвекции в камере установите тангенциальный вентилятор, наварив ему узкий выход и широкий вход.
- Вентилятор вставьте в камеру. Он будет забирать воздух вверху, прогонять его через ТЭНы, выгонять внизу, а затем распределять по всему объему камеры.
- ТЭНы установите вдоль параллельных стенок и соедините по распределению на фазы.
- ТЭНы закройте, оставляя открытым вентилятор, основная часть которого должна располагаться вне камеры (чтобы не оплавить обмотку).
- Установите электрощит. Правда, эту работу лучше поручить специалисту.
Полученное оборудование – камера полимеризации – будет иметь мощность 12 кВт на разогреве и 6 кВт в работе.
Важно! Энергоносителем в таких печах просушки порошковой краски может быть не только электричество, но и природный газ, и дизельное топливо.
Покрасочный инструмент – пистолет
Чтобы нанести порошковую краску на изделие, требуется специальное устройство. Это может быть краскопульт или пульверизатор. Но чаще всего это недолговечные, точнее сказать, одноразовые, пистолеты китайского производства. Так как в нашем случае все изготавливается своими руками в домашних условиях, такое устройство можно смастерить минут за 10. Такой пистолет прост в использовании, дешев и практичен. Переход с одной краски на другую занимает несколько секунд.
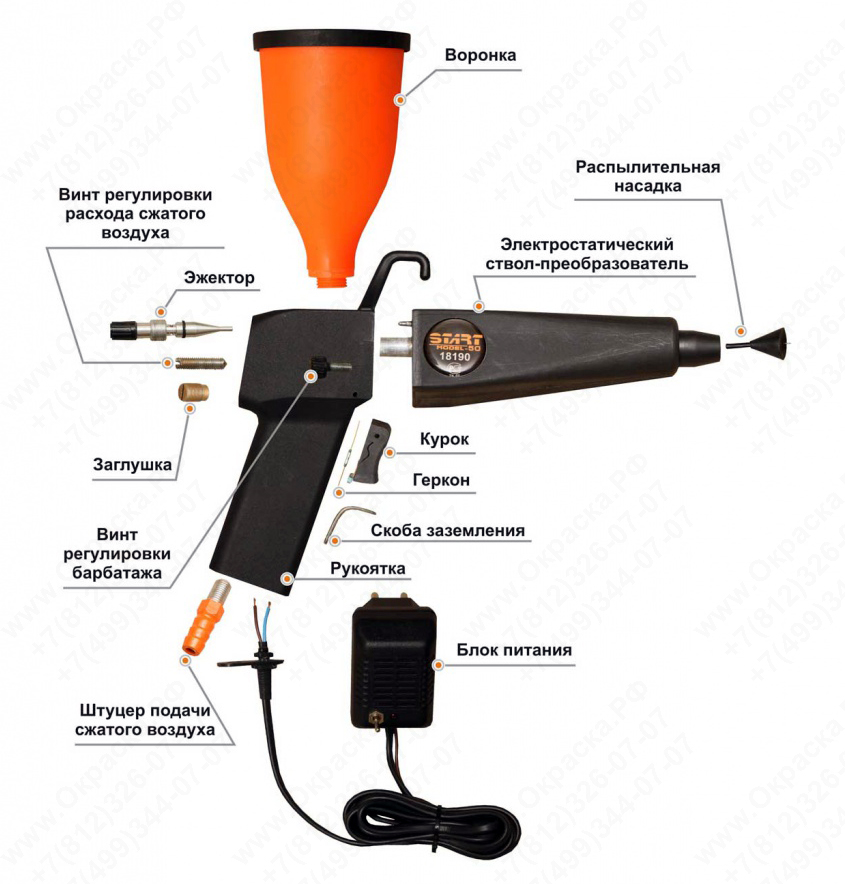
Как сделать пистолет для порошковой краски:
- Возьмите обычную пластиковую 1,5-литровую бутылку. Главное, чтобы она была сухая и чистая.
- Заполните ее на 1/3 порошковой краской, закрутите металлической пробкой.
- Проделайте в пробке маленькие отверстия. Чем больше отверстий, тем качественнее будет нанесение. Зачистите пробку снаружи от заусениц, оставшихся после прокалывания.
- Подключите к пробке проводом источник высоковольтного напряжения около 25 киловольт. Для этой цели лучше всего приобрести компрессор.
После всех манипуляций получается вполне приличный пистолет.
Мелочи, без которых не обойтись
Перед началом окраски нужно тщательно позаботиться о том, чтобы все операции проходили при идеальных условиях:
- Необходимо отличное освещение. Используйте лампы дневного света. К обычной лампе порошковая краска отлично прилипает.
- Нужна хорошая вентиляция с двумя моторами (на вход и выход). Дополнительно придется надеть марлевую повязку, а лучше профессиональный респиратор.
- Придется изобрести способ сбора остатков порошковой краски. На начальных этапах используйте старый мощный пылесос.
Когда все тщательно подготовлено, можно приступать к покраске своими руками нужных деталей.
Технология
Процесс окраски металлических деталей порошковыми составами можно разделить на три этапа. Это подготовка поверхности, непосредственное окрашивание (напыление) и закрепление результата (полимеризация).
Подготовительный этап
Он самый важный. От того, насколько качественно будет подготовлена к окрашиванию поверхность, зависит результат работы. Следуйте следующим инструкциям:
- Возьмите обычную чистую тряпочку и очистите всю поверхность обрабатываемой детали от пыли и грязи.
- Наждачной бумагой или специализированными металлическими щетками зачистите участки с коррозией.
- Обезжирьте растворителем деталь, это увеличит адгезию поверхности с краской.
- Проведите грунтование. Для этого покройте изделие краской на основе неорганических веществ. Благодаря этому слою сводится на нет риск проникновения воздуха, а также влаги под высохшую краску.
- Нанесите сверху детали слой, состоящий из соединений натрия и нитрата хрома. Этот процесс имеет название пассивирование. Он проводится, чтобы ржавчина не появилась в период подготовки детали к покраске. Все действия довольно просты, поэтому все можно сделать в домашних условиях своими руками.
- Просушите заготовку в самодельной печи.
Важно! Если деталь имеет слишком сложную конфигурацию, сильно загрязнена и покрыта коррозией, замочите ее в растворе щелочи.
Покрывание детали порошковым покрытием
Следующий этап после подготовительного – непосредственно окрашивание. Тут все довольно просто: поместите деталь в отсек напыления, закрепите и напылите ЛКМ.
Совет! Если с помощью окраски планируется достичь устойчивости детали к воспламенению, купите огнезащитные ЛКМ по металлу («Негорин», «Полистил» и им подобные).
После нанесения порошковой краски начинается процесс создания отвержденного полимерного слоя.
Полимеризация
Суть этого процесса в том, что окрашенная деталь устанавливается в специальную печь. Там она в течение определенного временного промежутка подвергается воздействию высокой температуры.
Для этого потребуется самостоятельно изготовленная печь для полимеризации порошковой краски. Чтобы процесс прошел без накладок, необходимо соблюсти следующие условия:
- Придерживайтесь рекомендаций, разработанных для каждой конкретной краски.
- Обеспечьте равномерное нагревание каждой детали.
- Соблюдайте точное время полимеризации. По его истечении извлеките деталь из камеры и оставьте на открытом воздухе для полного остывания.
Применение этого способа окрашивания порошковыми составами идеально подойдет тем, кто любит все делать своими руками. Делать самостоятельно печь для полимеризации довольно долго, однако на лицо существенная экономия средств и получение качественного покрытия.
Основная идея нанесения лакокрасочного покрытия с применением электростатического поля высокого напряжения заключается в том, что частицы с противоположными электрическими зарядами притягиваются друг к другу. Для нанесения порошковых красок подходит большинство термостойких токопроводящих твердых изделий, и прежде всего таких металлических объектов как:
- бытовая техника
- офисная мебель
- садовая мебель
- автомобильные принадлежности
- профили
- изделия из проволоки
- фасадные элементы и прочее
Порошковые краски - исходные продукты для получения полимерных покрытий. Это многокомпонентные системы, состоящие из твердых частиц - пленкообразующих и разделяющей их среды - воздуха.
Выпускаемые порошковые краски различаются по цвету (возможны все цвета по RAL), типу пленкообразователя (эпоксидные, полиэфирные, полиакрилатные, полиамидные и др.), фактуре поверхности порошковые покрытия (глянцевые, матовые, "муар", текстурированные, под "кожу", "мрамор", "гранит", "золото", с эффектом "металлик", "антик" и т.д.). По назначению порошковые краски различают для наружных и внутренних работ, для защиты труб, для получения химически стойких, антифрикционных, электроизоляционных и других покрытий; общего и функционального назначения.
Порошковые краски обычно поставляются с завода-изготовителя в полиэтиленовых мешках, вложенных в картонную коробку. Вес одной упаковки 20 - 25 кг. Как правило, порошковые краски промышленного изготовления, у которых не истек срок годности, пригодны для получения покрытий без какой-либо подготовки. В тех случаях, когда были нарушены условия хранения или транспортировки материала, требуется его переработка - измельчение и просев.
Порошковые краски, поступающие на участок, должны быть в закрытом виде, снабжены этикеткой, и иметь технический паспорт. Рекомендуемые условия хранения порошковых красок: в помещении при плюсовой температуре не выше 27 С. Типичные дефекты красок, связанные с неправильным хранением: комкование и агрегирование, химическое старение, увлажнение сверх допустимой нормы.
Порошковые краски - материалы промышленного применения. Они требуют специального оборудования для нанесения и формируют покрытия, как правило, выше 100 С (в основном 160-250 С), поэтому пригодны для окрашивания изделий из термостойких материалов.
Технологический процесс получения покрытий из порошковых красок включает три основные стадии:
-подготовка поверхности;
-нанесение порошковой краски;
-формирование (полимеризация) покрытия.
Качество покрытия зависит от соблюдения технологических режимов всех перечисленных стадий процесса. В каждом конкретном случае, под конкретное изделие разрабатывается свой технологический процесс. При этом в первую очередь, учитываются условия эксплуатации изделия и конструкционный материал, из которого он изготовлен.
От указанных факторов зависит выбор способа подготовки поверхности (обезжиривание, фосфатирование, хроматирование и пр.) и типа порошковой краски (эпоксидная, полиэфирная, полиуретановая и др.).
Линия для нанесения порошковых красок (покрытий) посредством распыления порошковой краски в электростатическом поле высокого напряжения обычно состоит из:
1. Многоступенчатой системы предварительной обработки поверхности,
2. Сушильной камеры для удаления адгезионной воды
3. Камеры нанесения покрытия
4. Камеры полимеризации порошковой краски
5. Транспортной системы.
Для небольших партий изделий или же при работе со специальными красками часто можно обойтись одной небольшой камерой для нанесения порошковой краски вручную, которая с учетом стоимости может быть размещена в любой производственной мастерской.
1. ПОДГОТОВКА ПОВЕРХНОСТИ
Подготовка поверхности при нанесении порошковых красок так же важна, как и при нанесении традиционных жидких лакокрасочных материалов.
Изделия, поступающие на окраску, не должны иметь заусенцев, острых кромок (радиусом закругления менее 0,3 мм), выступающих сварных швов, сварочных брызг, прожогов, трещин. Для очистки поверхности от ржавчины, окалины, старых покрытий рекомендуются механические способы (струйная абразивная обработка с применением дробеметных, дробеструйных и пескоструйных аппаратов).
В отдельных случаях рекомендуется продувка поверхности сжатым воздухом, во избежание малейших следов соринок на поверхности.
Перед нанесением порошка поверхность должна быть сухой, чистой без окалины и ржавчины, очищенной от всех загрязнений, консистентных смазок, масел и других загрязнений. Это осуществляется в установке для предварительной обработки, состоящей из нескольких зон. После соответствующей очистки следует чаще всего в зависимости от материала, травление, обезжиривание, фосфатирование или хроматирование.
Существует два основных метода химической обработки поверхности от загрязнения: окунанием в ваннах или распылением растворов в туннеле.
При обработке в туннеле предназначенные для обработки детали проводятся цепным конвейером через различные зоны обработки. Здесь применяются слабые фосфорнокислые соли щелочных металлов, кислоты и основания. В распылительном туннеле размещены распылительные контуры, равномерно обрабатывающие детали со всех сторон. Число сопел, угол струй и производительность насосов должны быть приспособлены к соответствующей детали.
Параметры установок для очистки металлических изделий, построенных по блочному принципу, должны быть рассчитаны на соответствующие индивидуальные случаи применения. Чрезмерные габариты приводят к перерасходу энергии и исходных материалов. В концепцию предварительной обработки должны быть в принципе включены мероприятия по эффективной защите окружающей среды и по переработке исходных материалов. Размеры и последовательность зон очистки могут варьироваться в зависимости от обрабатываемых деталей и с учетом специфических требований клиента.
2. СУШКА ДЛЯ УДАЛЕНИЯ ВОДЫ
После того как детали цепным конвейером пропущены через все стадии предварительной обработки, из них остается еще удалить имеющие остатки влаги. Это осуществляется в камере для удаления адгезионной воды. Она подобна печи полимеризации, но проще по конструкции и работает с температурами до 150 С. В зависимости от типа деталей может оказаться достаточной обдувка обычным воздухом из помещения. Однако в каждом случае нужно исходить из того, каких затрат потребует тот или иной процесс сушки адгезионной воды.
3. КАМЕРА НАНЕСЕНИЯ ПОРОШКОВОЙ КРАСКИ
В основе электростатического нанесения лежит принцип электризации частиц, находящихся в состоянии аэрозоля. Зарядка частиц достигается воздействием внешнего поля.
Различают два способа нанесения порошковых красок в электрическом поле - электростатический (с зарядкой частиц краски за счет источника тока) и трибостатический (с зарядкой частиц порошка за счет трения).
Наиболее распространенный способ нанесения порошковых красок - это электростатическое напыление. Этот способ позволяет наносить любые порошковые материалы (эпоксидные, полиэфирные, полиуретановые), в отличие от трибостатического, которым наносятся, обычно, эпоксидные краски, а остальные требуют специальных добавок. Электростатический способ нанесения краски обеспечивает получение хорошего качества покрытий и достаточно производителен. При электростатическом способе нанесения порошковых красок используются разные типы распылителей. Как правило, по одному каналу пистолета проходит (инжектируется) порошковая краска, по другому - сжатый воздух для распыления. В пистолете же происходит зарядка порошка при 60-70 кВт. Давление воздуха на распылителе 0,8 - 1,5 МПа (1-6 бар). Сжатый воздух должен быть очищен от следов масла, влаги и пылевидных частиц. Содержание масла в воздухе должно быть не более 0,01 мг/м3, влаги не более 1,3 г/м3, точек росы - не выше 7 С, содержание пыли - не более 1 мг/м3.
Для распыления на пистолете применяются различные распылительные насадки. Толщина покрытия за один слой 20 -150 мкм.
Распыление порошковых красок осуществляется в камерах нанесения. Конструкция камер различная. Принцип один - краска, не осевшая на поверхности изделий, отсасывается вентилятором и проходит через фильтр или циклон. Отработанный и очищенный воздух выбрасывается, а частицы порошка отделяются на фильтровальном элементе (ткани, бумаге). Далее не осевшая краска собирается в емкости или подается обратно на распыление в пистолет.
При смене цвета краски необходимо чистить или всю камеру или менять фильтр (фильтрующие элементы) и продувать шланги подачи краски.
Полнота осаждения порошковых красок зависит от удельного массового заряда частиц, конфигурации и размеров окрашиваемых изделий, скорости движения воздуха в камере нанесения и равномерной подачи порошковой краски. Поэтому важным является соблюдение требуемых параметров работы электростатических установок нанесения, окрасочной камеры и порошкового резервуара (питателя).
Параметры стабильной работы электростатических распылителей:
- Напряжение на коронирующем электроде 60 - 80 кВт;
- Давление воздуха на входе в распылитель 0,1 - 0,6 МПа (1-6 бар);
- Оптимальное напряжение при нанесении порошковых лакокрасочных материалов с различным типом пленкообразующих 70 - 80 кВт;
- При повторном окрашивании (перекрас) изделия напряжение на коронирующем электроде устанавливается напряжение 60 - 70 кВт;
Однако следует отметить тот факт, что все оптимальные параметры следует подбирать экспериментальным путем с учетом конкретных габаритов изделий и их конфигурации. Также немаловажным фактом для наиболее полного и качественного нанесения порошковых крсаок является выбор типа распыляющей насадки.
Порошковый резервуар (питатель) должен обеспечивать плавную и регулируемую подачу порошкового материала в пистолет в пределах 0-25 кг/ч и такую же подачу воздуха с расходом 0-20 м3/ч.
Несоблюдение требуемых рабочих параметров может привести к возникновению дефектов покрытий.
4. КАМЕРА ПОЛИМЕРИЗАЦИИ ПОРОШКОВОЙ КРАСКИ
При отверждении порошкового покрытия формируется структура его внутренних и поверхностных слоев. При этом характер поверхности определяется не только природой ЛКМ, но и условиями формирования покрытия.
Требуемые условия формирования порошкового покрытия указаны в технической документации, сопровождающий порошковую краску. Соблюдение режима отверждения особенно важно, поскольку любое отклонение от него неблагоприятно сказывается на свойствах получаемых покрытий. Недоотверждение (недогрев), влияет на механические свойства порошкового покрытия (покрытия хрупко разрушаются при ударе и изгибе), переотверждение (перегрев) - на цвет и блеск покрытия.
Обычно для порошковых красок существует несколько режимов отверждения. В зависимости от материала изделия и от условий производства можно выбрать тот или иной режим отверждения. Под температурой отверждения в документации значится температура на поверхности изделия, а не в камере.
Время нагревания (полного прогрева) зависит от толщины изделия, поэтому при навеске окрашиваемых изделий на подвеске необходимо учитывать толщину окрашиваемых изделий. Обычно при конвективном методе сушки время отверждения покрытия составляет 15-25 мин (температура 160-250 ?С).
Использование комбинированной сушильной камеры (с применением ламп инфракрасного излучения) позволяет сократить время отверждения покрытия до 10-12 мин. У такого вида камер есть все преимущества инфракрасной и конвекционной сушилки:
- Повышенная скорость подачи энергии и как следствие сокращение времени нагрева изделия;
- Не требуется предварительный нагрев деталей;
- Быстрый выход на рабочую мощность;
- Хорошая возможность управления и регулировки;
- Значительное снижение времени отверждения покрытия на тонкостенных изделиях;
- Не требуется большая зона охлаждения;
- Быстрое низковязкое оплавление порошка, что позволяет получать улучшенные механические свойства покрытия;
- Высокий КПД.
5. ТРАНСПОРТНАЯ СИСТЕМА
Устройства для транспортировки деталей служат для автоматизации процесса нанесения порошковой краски. При этом в первую очередь следует обратить внимание на подвесные и ленточные конвейеры. Многие проблемы транспортировки, в частности, при работе с не очень крупными или тяжелыми деталями решаются с помощью однониточных или подвесных конвейеров. Там, где требуется наносить покрытие на длинномерные или крупногабаритные детали, или же в тесных помещениях наилучшим образом подходит транспортная установка, состоящая из устройств с приводом и без привода (так называемая установка Power+Free), позволяющая осуществлять продольные и поперечные перемещения.
Следует обратить особое внимание на систему смазки транспортной установки. Температура в сушилке может достигать 250 С, поэтому необходимо применять термостойкие смазочные материалы.
Важную роль играет оснастка при навеске изделий на конвейер. Для каждого вида изделий следует подбирать наиболее рациональный тип подвески и вариант их размещения на ней. При наличии разнотипных окрашиваемых деталей необходимо иметь несколько комплектов подвесок. По опыту один комплект подвесок при подвеске на конвейер должен занимать как минимум половину его длины.
Комплектация деталей на подвеске осуществляется таким образом, чтобы детали не перекрывали друг друга, а расстояние их поверхностями было не менее 50 мм. Навеска деталей осуществляется также с учетом сложности конфигурации и возможности их прокрашивания за время прохождения через камеру.
Разработка конструкции подвесок проводится таким образом, чтобы поверхность деталей по возможности закрывала точки (крючки, штыри) навески деталей и тем самым препятствовала бы окрашиванию подвесок.
При неоднократном прохождении подвесок через камеры окраски и сушки происходит их неизбежное зарастание краской. Через определенное время по мере зарастания подвески необходимо очищать от старой краски. Подвеска очищается механическим способом или методом обжига в печи при температуре 400 С. Как правило, после обжига требуется рихтовка подвесок.
Существуют химические методы очистки подвесок от краски, например, травление в растворе каустика при температуре 80 С с последующей их промывкой и снятием размягченной краски вручную. Но, это сложный процесс, он требует приобретения специального оборудования.
По мере эксплуатации и очистки подвесок часто выходят из строя элементы навески для деталей (крючки). В большинстве случаев на разных предприятиях крючки к подвеске привариваются. При неоднократной навеске деталей на крючки, их обжиг, очистка приводят к ломке крючков и необходимости их замены. При сварном соединении этот процесс трудоемкий и не совсем удобный. Рекомендуется применение крепления крючков в отверстиях, что позволяет быстро их менять на новые очищенные.
Хранение подвесок обычно производится в определенном месте, с комплектованием их по видам и в подвешенном состоянии.
Пример окрашенных деталей
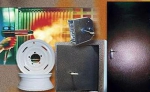
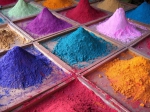
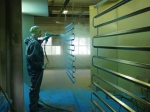
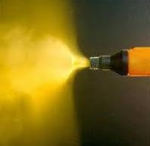
[ Нажмите на фото
для увеличения ]
Существует множество различных способов нанесения всевозможных покрытий на металл. Это и анодирование, и серебрение, и оцинкование, позолота, хромирование, а также обычная окраска металла с помощью лаков и красок на основе органических растворителей. Все эти покрытия наносят с целью защиты поверхности металла от коррозии, а также в декоративных целях. Покрытие поверхности стойкими к коррозии металлами - оловом, хромом, серебром - дорогой и трудоемкий процесс, а нанесение обычных масляных красок не дает долговечного и прочного защитного слоя.
Поэтому современная технология окраски использует другой метод - порошковое покрытие металла, который значительно дешевле метода нанесения благородных и инертных металлов и, в то же время, намного надежнее обычной краски.
Технологии
Огнезащита металлических каркасов зданий
При воздействии высокой температуры металлические каркасы зданий, состоящие из колонн и поперечных балок, быстро нагреваются
Порошковая окраска металла. Технология и оборудование
Порошковая окраска металла: на предварительно подготовленное металлическое изделие напыляется мелкодисперсный порошок